Automatic fly ash pelletizing machine
Introduce about automatic fly ash pelletizing machine
Automatic fly ash pelletizing machine is equipped with autoclave and screening equipment. Finished products are applied to the aggregates in commercial concrete, salt –resistant concrete, high strength concrete, concrete block, wall panel and so on
Technical specification of automatic fly ash pelletizing machine
Designed capacity | 100.000 m3/year |
Operating method | Spinning disc |
Rotary cycled time | 25 – 40 r/m |
Power | 129 kW |
Size of fly ash particles | 2.5 – 20 mm |
Warranty | 12 months |
Workers | 8 people |
Factory area | 4000 m2 |
Place of origin | DMC, Vietnam |
Technology description of automatic fly ash pelletizing machine 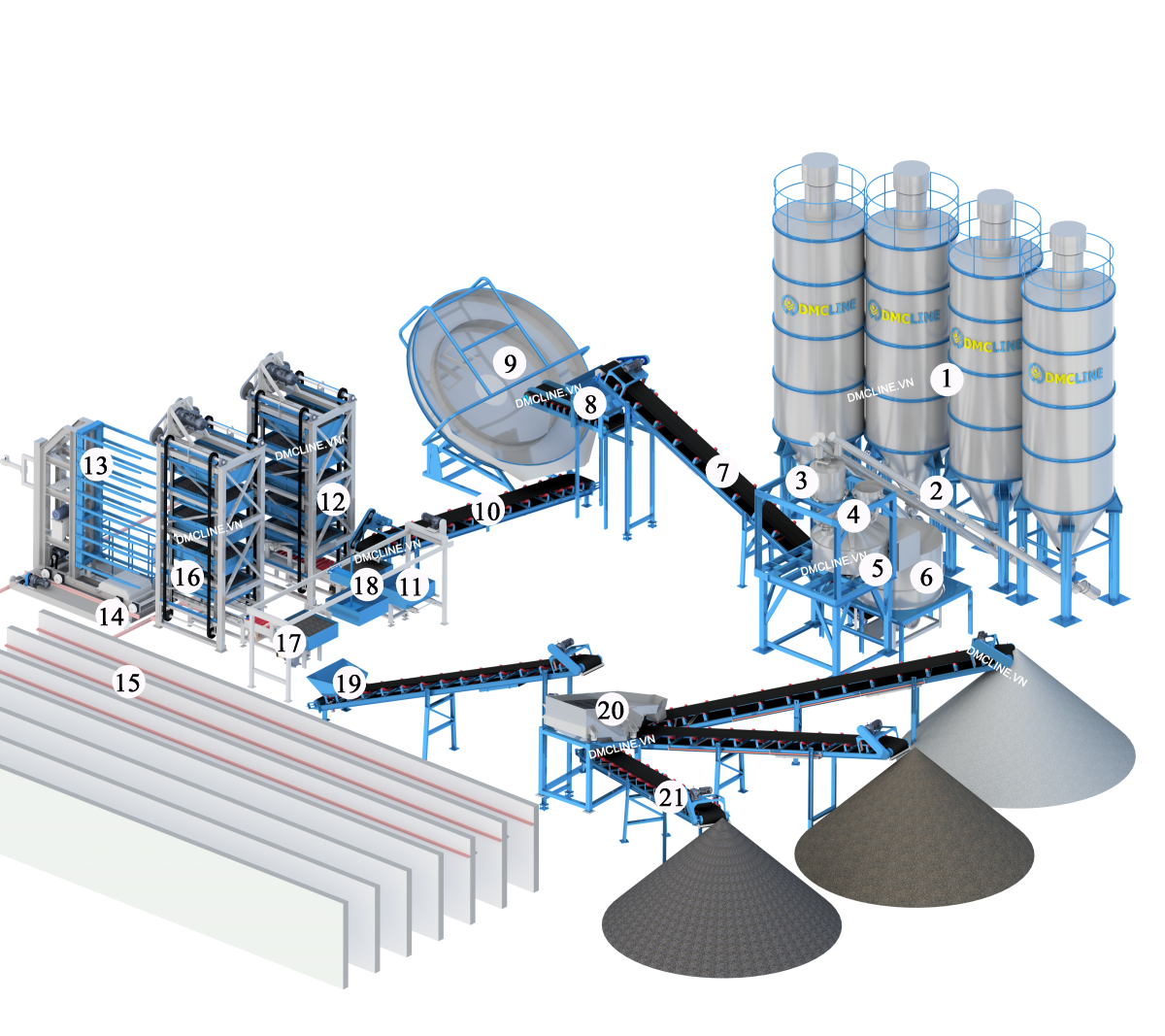
1. Silo: A special purpose storage contains cement. Besides the steady steel structure, it includes dust filtering system, anti-clogging aeration and safety valve.
2. Screw conveyor: transfer cement and fly ash from silo to the scale
3. Fly ash and cement scale: Include a bucket and a scale. Scaled data will be displayed on control center to help workers monitor the production process easily.
4. Additives and water scale: Include a bucket and a scale. Scaled data will be displayed on control center to help workers monitor the production process easily
5. Planetary mixer: Cement and fly ash after scaling will be mixed evenly as setting parameters
6. Anti-clumping mixer: the admixture of cement and fly ash will be mixed again to have the uniformity and anti-clumping.
7. Belt conveyor: transfer materials after mixing to material dividing machine
8. Material diving machine: Store and deliver materials after mixing to fly ash palletizer
9. Fly ash pelletizer: Use a circular motion to roll the ingredient mixture into particles of the desired size.
10. Belt conveyor: measure the particles for each tray
11. Tray conveyor: transfer trays containing particles to tray stacker
12. Tray stacker: stack trays into each story to help finger cart receive trays easily
13. Finger cart: Receive the trays containing particles and transfer to curing chamber; pick the trays containing particles to lowerator
14. Movement rail system: Transfer trays from tray stacker to curing chamber and lowerator
15. Curing chamber: Store and cure the particles to the desired strength and moisture
16. Lowerator: feed tray sequencely to particle separation machine
17. Particle separation machine: separate the particle from trays
18. Recirculating tray machine: transfer trays after separting particle to tray conveyor
19. Belt conveyor: transfer finished products to 2-stage vibrating screen to classify
20. 2-stage vibrating screen: classifies the particles in to 3 different sizes
21. Belt conveyor: transfer each type of particle from vibrating screen to 3 different storage yard
Production process of automatic fly ash pelletizing machine
B1: Cement and fly ash from silo are transferred to scale by screw conveyor. Additive and water are transferred to scale by water pump and additive pump at the same time
B2: Cement and fly ash after scaling as the ratio and discharge to planetary mixer
B3: Planetary mixer will mixed the mixture of cement and silo then discharge to anti-clumping
B4: In anti-clumping mixer, the mixture will be added water and mix well, anti-clumping then discharge to belt conveyor
B5: Belt conveyor transfer material to the material dividing machine
B6: Material dividing machine delivers the mixture of materials to fly ash pelletizer
B7: Fly ash pelletizer produces the particles with desired size and strength.
B8: The particles with desired sized and strength are transferred to belt conveyor and discharged to each tray
B9: Tray conveyor transfers tray in turn to the position of tray stacker. At the same time, tray stacker stack into each story
B10: Finger cart receives trays from tray stacker and transfers to curing chamber
B11: The particles are cured in curing chamber to have the desired strength and moisture
B12: Finger cart transfer trays after curing from curing chamber to the position of tray lowerator
B13: Tray lowerator lower each tray in turn to the position of particle separation machine to separate the particles from tray. At the same time, recirculating tray machine transfer tray after separating to the position of tray conveyor for the next cycle.
B14: Belt conveyor transfer particle after separating to vibrating screen to classify
B15: Vibrating screen classifies the particles into 3 different types
B16: The particles after classifying will be transferred to storage yard by belt conveyor.
Related products
Low price fly ash pelletizing machine with high quality. 01 year warranty. Fly ash palletizer manufacturer?